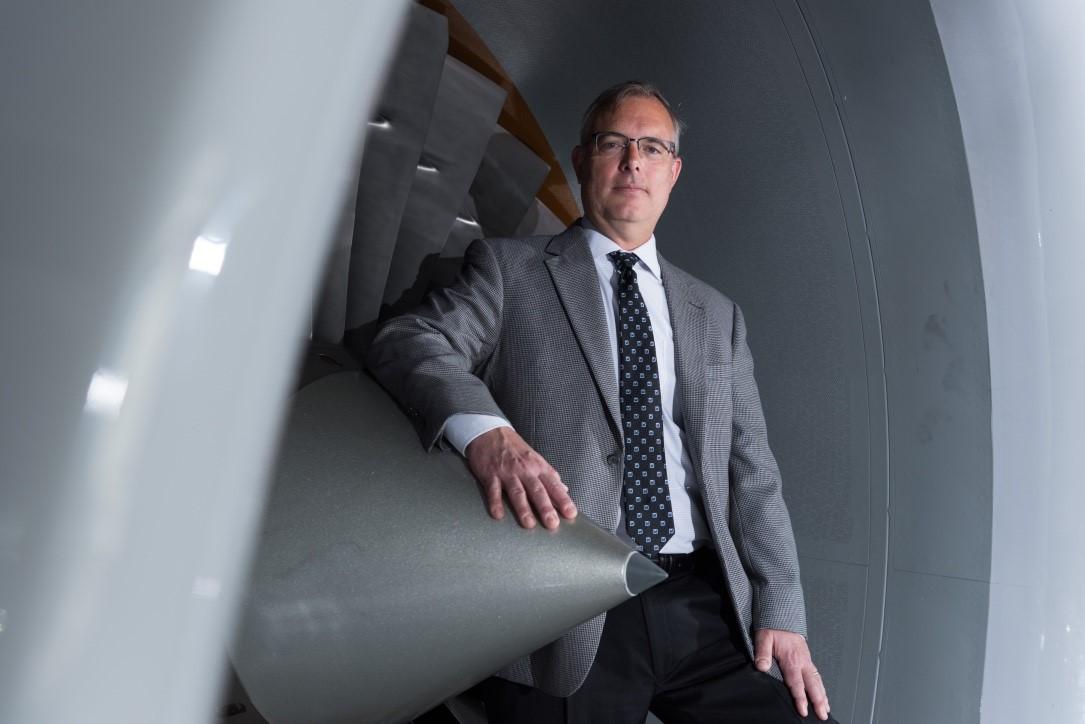
IMat Initiative Lead Q&A: Richard Neu
April 27, 2023
By Laurie Haigh
Richard Neu leads the Materials in Extreme Environments research initiative for the Institute for Materials at Georgia Tech. In this role, he is working to engage and build an interdisciplinary research community to address the complex issues associated with new materials in extreme environments. These environments include high temperature, high pressure, corrosive, wear/erosion, cyclic loading, high-rate impacts, and radiation. Neu is also a professor in the Woodruff School of Mechanical Engineering with a courtesy appointment in the School of Materials Science Engineering and director of the Mechanical Properties Characterization Facility.
In this brief Q&A, Neu discusses his research focus, how it relates to materials research, and the impact of this initiative.
What is your field of expertise and at what point in your life did you first become interested in this area?
My field of expertise is the mechanical behavior of materials, mainly structural alloys. As an undergraduate at the University of Illinois, I chose to study engineering mechanics, which is the discipline explaining the way materials behave under loads and displacements. This led me to conduct undergraduate research on the thermomechanical mechanical fatigue of railway wheels, which occurs from the brake shoe application on the tread resulting in frictional heating of the wheel's surface. On a long downward grade, the wheel treads can get red hot, since the brakes are continuously applied. The strength and elastic properties of the wheel steel are reduced, and permanent changes such as the formation of residual stresses and changes in the microstructure degrade the mechanical behavior after repeated braking. Understanding and predicting this response enables more durable wheel steels and designs.
In my early career, I investigated several problems that involved structural materials needing to survive extreme environments. These included the understanding of the mechanisms leading to hot bearings in railway freight cars, the thermomechanical response of the skin material for hypersonic aircraft, and the thermomechanical fatigue and creep of hot turbine sections in gas turbines for both propulsion and energy generation. These problems are changing because high strength, high creep resistance, and good fracture toughness are needed, while the material itself continues to evolve at these high temperatures. In addition, chemical reactions can occur, significantly affecting the microstructure and mechanical behavior of the material near the surface. The problem of understanding these materials operating in these extreme environments entails a multidisciplinary approach involving mechanics, metallurgy, manufacturing processes, tribology, and machine design.
What questions or challenges sparked your current materials research?
My current research does not deviate much from my early days of research. The most challenging problems in the mechanical behavior of materials involve pushing materials to their extremes. There is a continuing need to discover and design structural alloys and composites with improved high-temperature properties, with reduced degradation in the environment they must withstand, whether corrosive, cryogenic, high temperature, or more often, a combination of these. Today, these challenges include developing more efficient gas turbine systems that can burn alternative fuels such as hydrogen, rolling bearing and gear steels that have higher reliability, and establishing quality assurance for materials manufactured using additive manufacturing and other novel processes to ensure that they will survive these extreme environments.
Why is your initiative important to the development of Georgia Tech’s Materials research strategy?
Leading the initiative for Materials in Extreme Environments, I desired to bring together faculty and researchers working in this area and those working on applications that involve materials operating in extreme environments. This year we identified one important application area where Georgia Tech is taking the lead. Hydrogen is likely to be a major player in the future green energy economy. One challenge to realizing a hydrogen energy economy is the efficient and low-cost generation, storage, and transport of hydrogen. In alloys, the degradation due to hydrogen embrittlement is one of the concerns that must be addressed. Both the materials understanding in this environment and the design of newer materials and surface modifications are needed. Furthermore, this needs to be accomplished at a large scale and low cost.
What are the broader global and social benefits of the research you and your team conduct?
The work we do enables safer and lower life cycle costs of mechanical systems, critically important for all the highly loaded structural components of aircraft and other transportation systems, hypersonic aircraft and rocket systems, gas turbine systems, nuclear power generation systems, and immense wind turbine components, as well as materials used in medical devices that are implanted in humans. Our research provides the knowledge and engineering tools to achieve a safer world and superior mechanical systems that improve the quality of life.
What are your plans for engaging a wider GT faculty pool with IMat research?
We are engaging with external experts to understand the needs in materials for the hydrogen value chain. While much research today is focused on producing green hydrogen through lower cost electrolysis and using hydrogen for energy generation with fuel cells, a big challenge of storing and transporting the hydrogen from its production to where it will be used requires novel solutions and materials. This involves, for example, storing hydrogen under extreme pressures in an environment where hydrogen itself can react and degrade the mechanical properties of the materials. The time is right for a diverse group of faculty to work on the storage and transportation challenges to facilitate energy having a substantial reduction in the carbon footprint while also reducing the life cycle costs of the infrastructure.